Nancy Brownell Gay tell us about the VEOX PMO mixproof valve
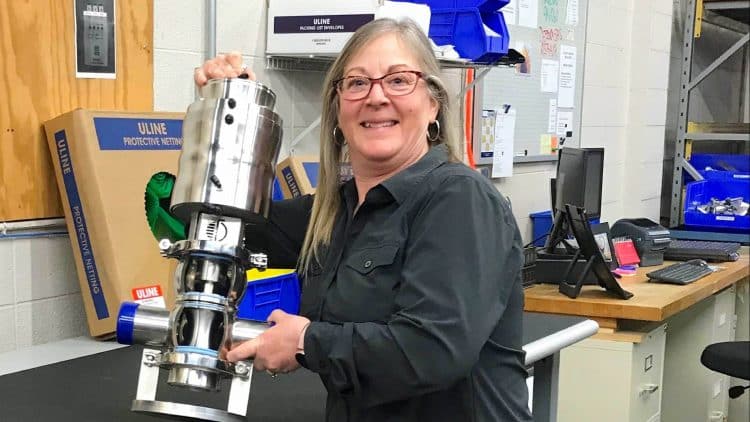
Nancy Brownell Gay, Regional Sales Manager for Definox Inc., New Berlin, Wisconsin, explains how this technology, the VOEX PMO mixproof valve, works and the benefits for Definox’s customers. Interview.
Nancy, could you please introduce yourself and tell us what you do at Definox?
I am Nancy Gay and I am a Regional Manager at Definox in the US. I manage the business for the Western US.
Our business in the US, we often go through distribution, versus on a direct basis. We work very closely with distributors to promote Definox products. We also do some work with original equipment manufacturers, or OEMs.
VOEX PMO double independent plug mixproof valves are presented as a new technology. Could you please explain how this works exactly?
The PMO mixproof valves are utilized in the US specifically for dairy facilities. PMO is a pasteurized milk ordinance, so it’s a safety regulation that the US has instilled into any valve that is utilized in milk processing and if it’s a mixproof valve, it has to have what’s called this PMO standard recognition.
What a mixproof valve is capable of, is transferring multiple fluids at the same time for the process. So, a customers can have two different types of products, say a standard milk product and a yogurt product being utilized at the same time or even a cleaning product and a milk product at the same time, can be processed using a mixproof valve.
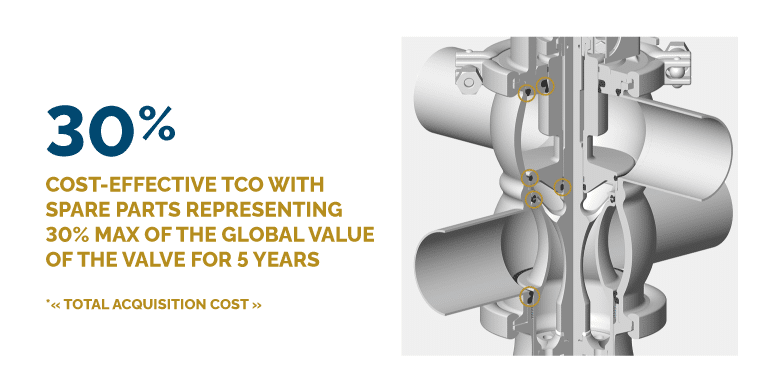
Do you have any other examples of how a mixproof valve is used?
Yes, In a Yogurt facility where they utilize different recipes for the product. Maybe they have a strawberry, and they have a lemon: you can have both products being used at the same time and there will be no cross over into one product into the other. So, where there are multiple storage tanks in the facility these mix proof valves will open and close based on the product that they want to transfer say from one tank to the filling line. They’re also operating another tank to another filling line. So, they can do multiple lines at the same time.
It assists the facility to reduce the size of their plant, have less piping in the plant, and increase their efficiency because the amount of product that is produced can be increased… because there is less waste and probably less cleaning solution is used as well.
How does the new version of definox mixproof valves specially meet us dairy process requirements?
The US has a PMO – Pasteurized Milk Ordinance, which is standard for safety and hygienic processes. In that technology, there are three seals in our process and if there’s a failure on a seal in the upper line, there has to be a secondary seal. That will be used to make sure there is no contamination across from one line to the other line. So that, where the valve is designed to have a safety feature that will not allow any cross contamination. It is an ordinance that has been in place for twenty years at least, so it’s not a new technology per say.
Our design is new in a sense that our valve has fewer welds and fewer seals that are used. So, our technology is less complicated, I’m going to say, than some of our competition.
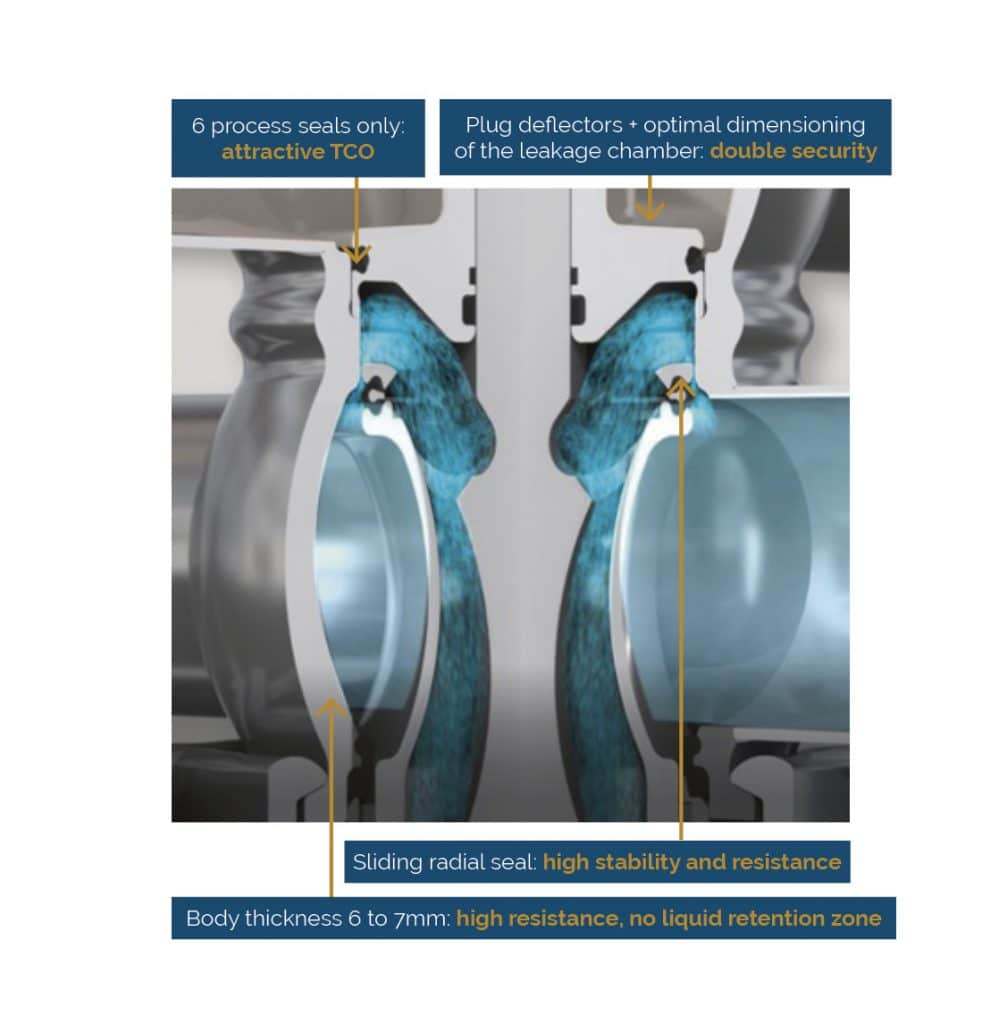
What are the main innovative features of the valve compared to other valves on the market
Because the Definox valve is made from bar stock the main innovative features would be fewer welds and seals used in our design, and thus less exposure to the process.
It’s challenging because there are some features of the product that are unique, but the valve has to meet this PMO ordinance and all the valves have to meet that particular requirement.
This PMO version is particularly suitable for dairy processes. Considering the high level of requirement for dairy equipment, is it suitable for all types of fluids?
Yes, other fluids can certainly use VEOX PMO mixproof. In a sense that if a customer has multiple types of fluids used in their process. They can use a PMO valve in multiple locations. So, they may be able to have less inventory or you can have fewer seals in your inventory as well. Perhaps, that would be a benefit.
What other benefits are there for Definox’s customers?
Our valves are maintainable and repairable. Some of our competitors, their actuators for instance, cannot be repaired. So, if a valve has a seal failure in the actuator, they have to replace the entire actuator, which is very costly and expensive to do. Then you have to basically throw away the actuator. Where in our valves, it’s a sustainable product from an environmental standpoint.
So, you can reuse the actuator by introducing new seals to the product. So, for the customers that want to be sure they are becoming more sustainable within their process, our valves will be able to accommodate for that. It is repairable so then the expense long term for them goes down because they don’t have to set up a new actuator, they can repair and use the same actuator. So, from a cost standpoint long term, it’s a benefit. Both from the inventory standpoint and ease of use standpoint.
I have been at facilities that used a competitive product and they had failures on actuators, and they had many, many of the actuators fail. It WAS a very time consuming and expensive process to reinstall new actuator on their valves.
Would you have anything else to share about the Definox’s technology?
There are also multiple plugs that can be utilized in the valve itself. So, if a customer has a high temperature application, they can utilize what’s called a “peek plug”. It’s interchangeable to the other plugs that are used in the valve. It’s a feature that, they can utilize the same valve. Many of the seals would be.
The same, especially in the actuator, so, you can have commonalities of products across their line from different types of applications.
What is your opinion about Definox in general?
Definox is very easy and simple to work with. It’s very customer focused and nimble, meaning that we can often create products that can solve problems for customers that have very specific applications. And we’ve done that for many customers. I know I have had that for Proctor and Gamble for instance where we needed new seals, we designed seals specifically for their type of product and accommodated for various requirements they may have. So, I think our ease of doing business together with customers is one of our priorities and I think we do a very good job in that realm of business.
We have multiple technologies for valve solutions, so I think the number of different products that we have in our product line, allows a customer to have a creative solution across many different types of applications.