Nicolas Czerniak : “TCO* is a real issue for our customers”.
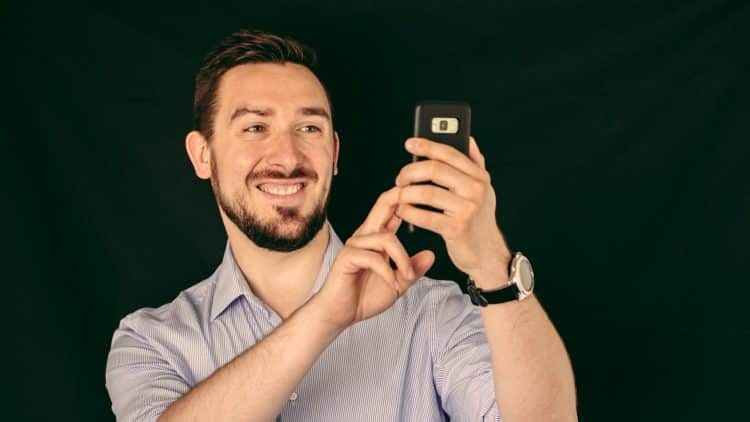
*TCO: Total Cost of Ownership
Nicolas Czerniak has been Regional Sales Manager for the Eastern European market and the Commonwealth of Independent States for 8 years and is responsible for key international accounts. As part of his sales missions, he is particularly aware of the economic and technical challenges faced by manufacturers. Interview.
Nicolas, why is Definox positioning itself and committing to the Expertise theme?
“Definox offers top-of-the-range products with expertise focused on the strength, robustness and durability of its products. This choice of positioning enables Definox to be highly competitive with other market leaders.
At Definox, the parameters and processes make the product better. When it comes to expertise, it is valuable to explain our method and to share Definox’s industrial know-how more extensively. Mass machining of components and hyper-quenching are industrial processes that use thicker bodies for longer valve life and greater durability.”
Can you explain what TCO is, and why it is a key issue for all manufacturers?
“TCO is the sum of capex and opex which are capital expenditure and operating expenditure. Total Cost of Ownership. This is the total cost of an item, including the initial purchase price, wear and tear, and the costs of using it throughout its life cycle.
Definox relies on high product quality to maintain a better TCO than the competition. With us, a valve is bought for several decades, so it is very important to keep the TCO under control.”
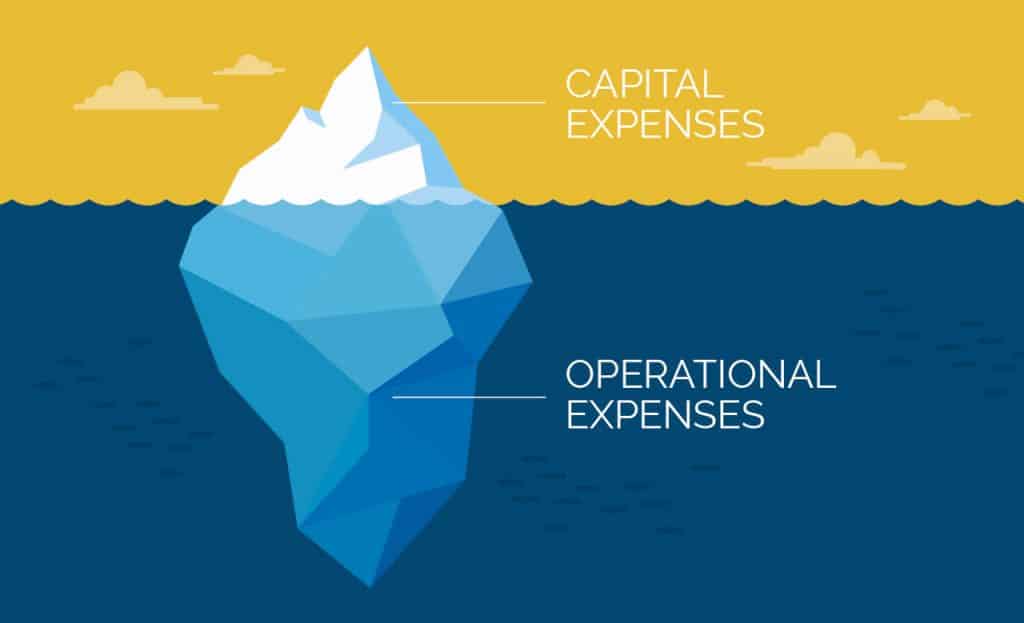
How does Definox help its customers control the TCO of their processes?
“TCO is a real issue for our customers. OPEX costs need to be contained because they can explode. They must be factored in. Having an attractive purchase price is good, but it’s not enough; you also must keep an eye on the cost over time.
Controlling TCO is a concept that is considered right from the design stage of our solutions, including in the choice of materials.
For example, we have chosen to design actuators that can be dismantled and maintained. Firstly, in the context of environmental issues, we can no longer afford to throw away components. Secondly, for the customer, changing an actuator represents perhaps half the initial cost of the valve. In the case of a Definox valve, however, the OPEX impact is low – it’s just a matter of changing a seal or a spring.
When we design a valve, we try as much as possible to work with existing parts to limit the number of part numbers. Definox ensures that the cost of repairing our solutions does not exceed a nominal value. We reasoned that above 30% of the initial price of the valve, the customer would not repair it but replace it. And we always try, even on a valve that is no longer on the market, to not exceed this percentage. It is allow the customer to keep his equipment and its performance.
We also have an after-sales service to support customers anywhere in the world, to ensure that their TCO remains high over time and, if necessary, to retrofit old-generation valves with new technologies.”
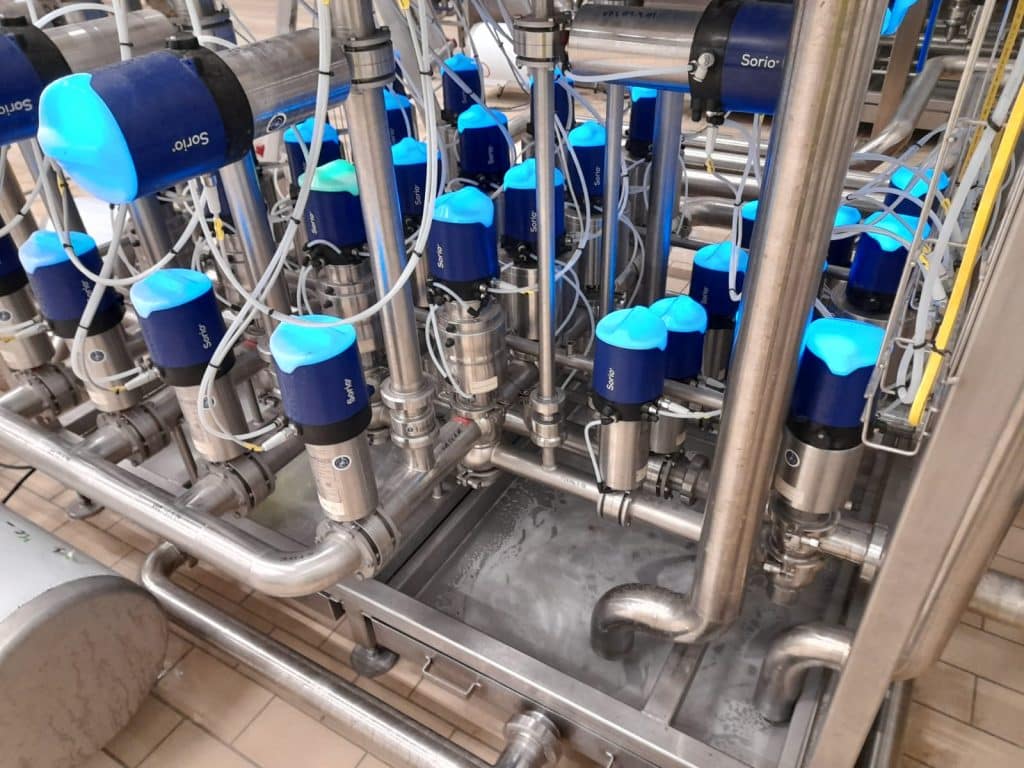
Do you have an example of a retrofit?
“Yes, I have several. We had an interesting case with an old manifold from the 1990s. We took it back, fully checked it and upgraded their system with new control boxes. Bringing new functions to systems that have been installed for a long time is a real advantage for customers, who can benefit from new technology without having to change their entire system. They can therefore limit the economic impact of an upgrade on their business.”
What improvements do you think could be made in the future?
“Definox aims to make life easier for its customers by giving them quick and instant access to the information they need to use and maintain their valves. This is achieved through the augmented reality application, videos, remote training, etc.
But also, as an expert, you need to be up to date with current standards and regulations. Because they change regularly, and because our business is a technical one. It is essential to keep abreast of the latest developments, to keep up to date with the latest training, and to strive for continuous improvement.”