Pigging system : The industrial innovation fusing productivity and the environment
Avoiding raw material loss, making the cleaning process in industrial transfer circuits easier, limiting the cleaning process’ impact on the environment, and optimizing the availability of production lines for industrial sectors such as: the foods industry, cosmetics, and chemicals, have become of major importance. Thanks to technological innovations in pigging systems, there are both standard and bespoke solutions dedicated to and easily beneficial to all these sectors.
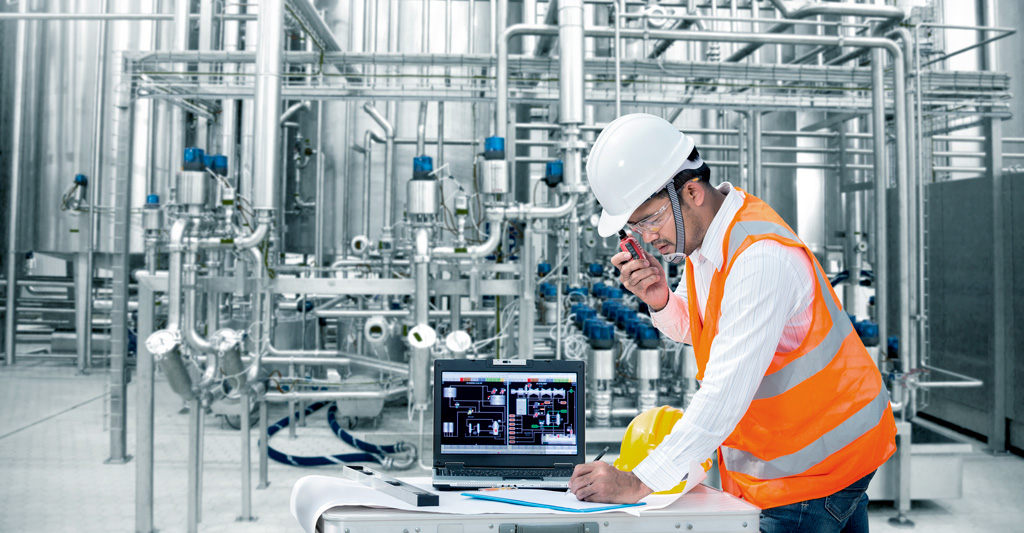
Loss of product output from the production line without a pigging solution
At the end of a transfer cycle, production lines without a pigging system can accumulate a considerable amount of product, thus generating a loss of the product and the need for reinforced cleaning. Besides product loss, there are also monetary and environmental costs due to the consumption of water and detergents needed to eliminate any trace of the product. Without a pigging system line shutdowns during the cleaning phase are longer.
The usual method consists of cleaning the lines after a production cycle using concentrated cleaning products. This method generates significant product loss, notably caused by the substances and treatments released in the effluents. The result is a large monetary and environmental impact from retreatment costs of the wastewater. A pigging system limits the product entering the sewage system and helps to reduce local taxes.
Pigging system Innovation to avoid wastage
Over the last few years innovations in pigging systems have remedied this phenomenon by limiting waste from liquid or pasty products thanks to less rejection. This allows for the valorization of the residual mass, with monetary gain because of a pig pushed through the pipes by a fluid.
The scraped product is recovered near the end of the line. Completely sanitary, this pigging system facilitates cleaning and reduces water and chemical product costs with less impact on the environment.
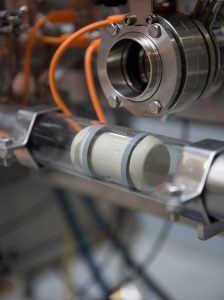
The pigging system used on production lines also allows for an increase in product yield by reducing changeover times and shutdowns for cleaning in place ‘CIP’.Once the pipes have been scraped and cleaned, the line is ready for a new production cycle. Thus, a safe, rapid production resumption using less cleaning products.
This pigging system is adaptable to all installations, which allows for recovering the product despite complex piping layouts or severe servicing conditions. It is an excellent ally for preserving the environment because It limits the release of pollutants and reduces water treatment station costs. It increases production globally, while optimizing and thus adding value to each production line in the plant.
A multi-industrial pigging system
These pigging systems are used with liquids and semi liquids of different viscosities, with no risk of damaging the product. Many sectors are interested in its use from the Food Industry (dairy, jams, chocolate, pet food…), perfumes and cosmetics, hygienic products (toothpaste, shampoos, shower gels…) household products (cleaning products, detergents…), or chemicals (paints, lithium batteries…).
These sectors benefit from increased hygienic safety of the production lines by avoiding contamination from the cross-over of different production cycles. These sectors also see a gain in flexibility by being able to treat several product types one after the other on the same production line.
In real terms, without a pigging solution, a 200-meter-long line can accumulate up to 600 liters of residual product that washes down the drain. A tangible financial loss… multiplied by the number of production lines found in the plant…multiplied by the number of plants. The cost can easily come to several tens of thousands of Euros each year, without including the extra cleaning costs added to the final invoice.
A pigging tool guarantees a rapid return on investment
Pigging system technology is based on the scraper which is detected by a magnetic field, delivering a possible product recovery of up to 95%, and more if the settings are optimized. Thus, a significant reduction in costs and expenses: Cleaning and treatment (fewer cleaning products, less waste), optimization of energy consumption (less water used, and less water wasted). A winning equation with a visible return on investment in less than one year.