UPCYCLING, A RISING VALUE FOR MANUFACTURING CHALLENGES
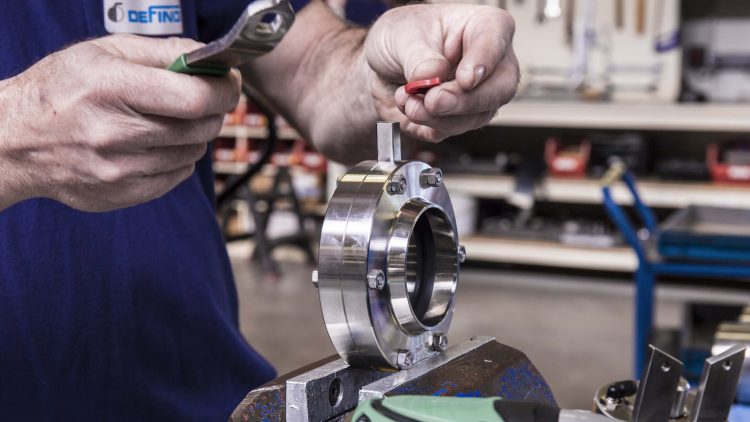
Just as expertise, safety or hygiene, the environment is a major preoccupation with manufacturers. Being in phase with the reality of the market, Definox has always anticipated, and proposed solutions adapted to the needs of its clients. The last few years have seen the rise of new concepts reflecting these needs. Among them, ‘upcycling’ meaning recycling or recuperation. Like sorting, waste management or reusing products, all practices that are virtuous and respectful of the environment. How is this an emerging idea in the industrial sector ? How has Definox always integrated it into product design and how does it illustrate it concretely ?
UPCYCLING, the new trendy concept
Intrinsically linked to environmental issues, upcycling consists of recovering a used object or product and transforming it to give it a second life and a new more efficient use.
If it has been in use in the textile industry for many years for example, whereas, technical industries have been, for some, in the early stages of putting the concept into practice. Not all of them were born with the idea of designing reusable, maintainable, repairable products.
In a broader sense, we need to look from the side of the users, consumers / customers. Society is waking up to ecological awareness, including for industrial equipment such as valves. Practices are changing and recycling is becoming the new credo for many of them.
Upcycling is developing significantly within brands and being integrated into corporate policy. Definox’s industrial clients appreciate working with companies that share the same values. Responsible purchasing and sustainable consumption. These issues are gradually gaining a place among industrial manufacturers.
UPCYCLING, THE NEW INTEREST OF MANUFACTURERS
Manufacturers are becoming aware that they can no longer work, design, and develop products without taking into account repairability and sustainability of the product. Ignoring this is to go against the current of good practices, be closed out of certain markets, and the risk damaging brand image.
Recycling is …. less Material waste, reduction of production costs, economies of energy, and preservation of the planet. It is important that companies mobilize against material waste and for the global economy of their sector. Wouldn’t this be beneficial to all companies and people ? Companies that produce elements and parts on a large scale, such as Definox, must consider the stakes to respond to product demand and sustain their business. They must lead by example.
UPCYCLING… INTEGRATED INTO PRODUCT DESIGN
For many international companies, standardization and industrialization of new concepts such as upcycling, takes time. If Definox has integrated this concept since its creation into the design of its valves and components, it is now time to accompany and support our clients in this process.
Definox’s customers and users are looking for product performance, safety, and sustainability. Definox has always worked within these objectives. As proof, preserving resources starts with the fight against obsolescence. That is why Definox valves are 100% repairable with standard maintenance tools.
From the beginning all products have been designed by our R&D department to be entirely maintainable. The modular aspect is essential. In real terms the pneumatic actuators are found on all varieties of our valves and are totally dismantlable so that only the necessary parts need be replaced. If the customer wishes to change certain valves or upgrade equipment, they can do it while keeping their actuator.
Definox also integrates retro-compatibility into its new development projects. The oldest valves have available spare parts allowing updating of customer equipment at the fairest environmental and economical cost. The adaptability and sustainability of Definox products is illustrated by the SORIO® control top that adjusts to all valves, even our competitor’s valves. A Definox exception.
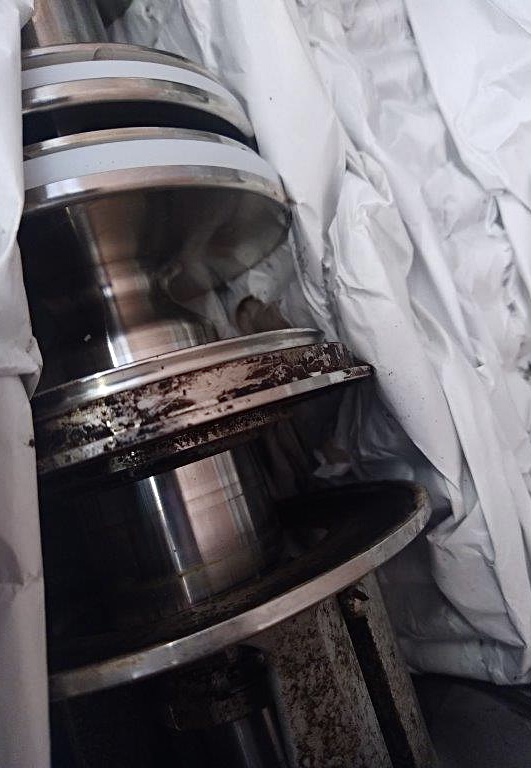
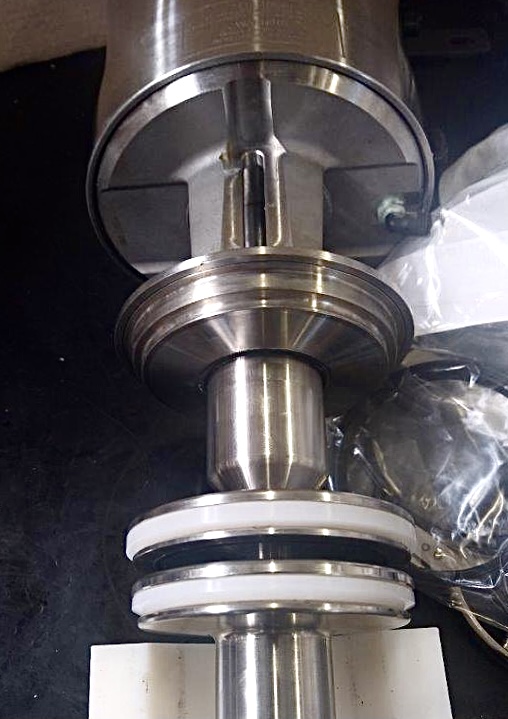
RETROFITTING, AN EXAMPLE OF RECYCLABILITY
Not all manufacturers have a vision of the technical possibilities of upgrading their processes and production lines. Thinking about recycling and retrofitting, gives you the possibility of investing in new lines and new equipment while ensuring cost optimization.
Definox is currently participating in a retro-fit project comprising hundreds of valves to maintain. It is a great example of what is possible thanks to the Definox product range. Here are the steps necessary for the proper renewal of equipment.
First, the preparation phase, where a technician goes to the customer. In the framework of a transfer of a repair grid (or manifold) from one manufacturers site to another, each valve in the grid was dismantled on site to be taken to the Clisson site. Before shipping the valves and shut off sections to be changed, the Definox technical teams took care to ensure the pairing of the valves at the customer’s site to guarantee the traceability and therefore the proper emplacement of the parts after repair.
This retrofit concerned several types of Definox standard valves (butterfly valves, fractional valves, and pigging systems ). Each piece of equipment was carefully checked for components having contact with liquids before overhauling the sections and changing the worn parts (process seals, actuator seals and springs). Everything was manually cleaned, checked for damage or scratches, then replaced or refurbished to new condition. The replacement of the other damaged parts was made as accurately as possible. This retrofit illustrates the intrinsic philosophy at Definox in opposition to the planned obsolescence of parts and equipment.
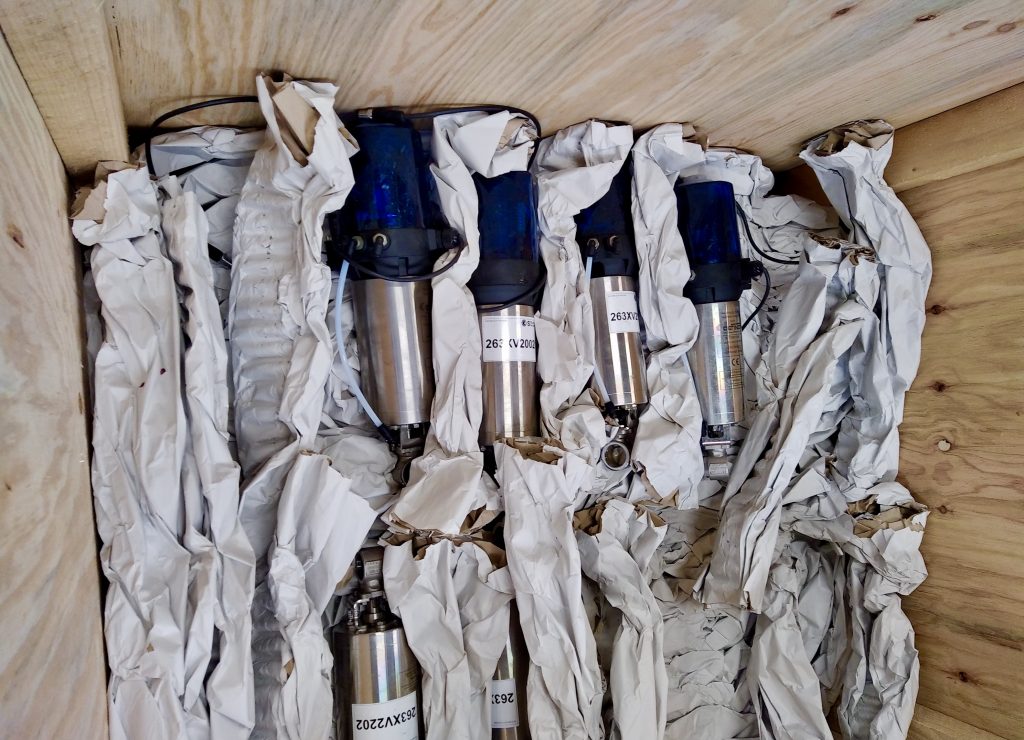
DEFINOX GOES BEYOND UPCYCLING
Created in 1968 by men determined to diversify their activities, Definox international has thought out its entire product range through the prism of optimization and sustainability.
Beyond integrating upcycling in its designs, Definox commits to reducing its packaging and waste, another aspect that confirms the virtuous ambitions of the company. Reducing one’s imprint starts with the awareness of logistics processes. All Definox packaging must guarantee effective protection of the equipment during shipping around the world, while limiting excessive packaging materials. A real challenge. In the process of reducing packaging volume, with equal protection, bubble wrap has been replaced by recyclable and biodegradable kraft paper.
91% of waste is recycled or reused
Today, to continue to respond efficiently to the challenges of its customers, Definox innovates. Going even further, Definox has decided to speak out and position itself on the issues of interest to manufacturers: expertise, safety, hygiene, and the environment. This is how the “DNA approach” came about, a space dedicated to developing the four themes through articles, data, testimonials… By supporting its customers this way, Definox continues to reflect on its business sustainability.